This is being driven politically by the EU’s “Green Deal”, among other things, which aims to make Europe the first climate-neutral continent by 2050. Net greenhouse gas emissions are to be reduced by at least 55% by 2030 compared to 1990. In this context, industry and medium-sized manufacturing companies must take a leading role and move towards climate neutrality.
It is therefore important for companies to scrutinize and optimize internal processes. Ecological sustainability in production cannot be credibly implemented without IT and cannot be realized quickly enough. Intelligent software solutions for the manufacturing industry, such as Manufacturing Execution Systems (MES), based on the Machine Data Acquisition (MDA) and Production Data Acquisition (PDA) modules, play a fundamental role in this.
Proven Tools for More Sustainable Production – MES Modules Machine Data Acquisition (MDA) and Production Data Acquisition (PDA)
A Manufacturing Execution System (MES) is a system in operational production management. The core tasks of MES include Machine Data Acquisition (MDA) and Production Data Acquisition (PDA).
Machine Data Acquisition (MDA) analyzes and visualizes machine data recorded in real-time in clear reports. This allows weak points such as faults or short downtimes and key figures such as OEE in the production process to be reliably recorded and visualized in reports.
The Production Data Acquisition (PDA) module provides effective support in the management and processing of simple to complex production orders. Recorded information is clearly presented to users. They can view order and article data, scrap values, comparisons of target and actual data for production or setup data at will – paperless, of course. The MES provides a digital image of production, enabling real-time monitoring of production processes.
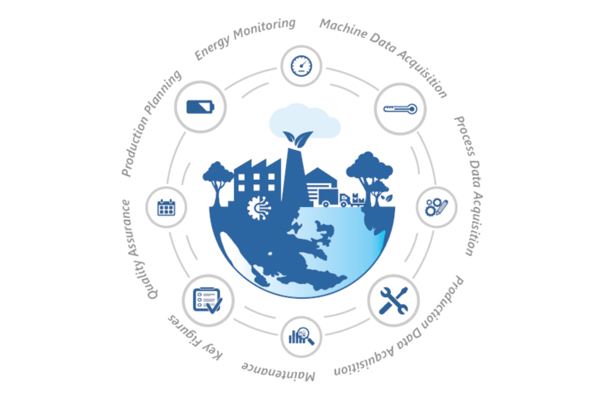
Transparent digital data in real-time directly from the store floor forms the basis for answering questions about production efficiency, rejects, resources used and product quality. This is the only way to make fact-based decisions in order to optimize existing processes and make production in the company more sustainable.
Once these core modules have been implemented, the MES can be individually expanded step by step and as required with additional modules such as Quality Assurance, Production Planning, Traceability or Maintenance, as well as many other Additional Functions. This interaction results in a wide range of options for optimizing production towards sustainability goals, which are always economic goals as well. In addition, seamless documentation becomes a piece of cake.
1) Identify Optimization Potential and Increase Resource Efficiency
Digitalization makes a fundamental contribution to increasing efficiency – right from the manufacturing stage, during packaging and through paperless production.
Efficient production is sustainable. An MES is indispensable for identifying optimization potential in production, as it provides the necessary key figures directly from production. Reports are necessary in order to:
- minimize raw material consumption
- reduce energy consumption
- avoid rejects and other material waste
- plan production processes precisely
By analyzing the recorded data, such as the quantity or quality of the products, sources of error in the production process can be identified at an early stage and any need for action can be specifically recognized. This enables production management to ensure quality and reduce rejects, for example. The MES also provides the data required for further systems to monitor energy consumption and costs and identify energy losses. Companies can then take targeted measures to increase energy efficiency, reduce emissions and document consumption with key figures.
2) Objective Data Makes Sustainability Reports Credible
Reporting obligations for industry and small and medium-sized enterprises are increasing. The high requirements can only be met with software support. By using an MES, manufacturing companies can fulfill their documentation obligations more easily, efficiently and accurately.
The data collected by the MES from the store floor facilitates the certification process, provides evidence of compliance with certain standards and enables credible reporting.Efficient production is sustainable.
3) Best Practices
130
Dr. Willmar Schwabe Group: The software solution provides the optimal data basis for optimization projects. The data is discussed at regular meetings of the store floor team. As a result, over 130 optimization projects have already been successfully implemented. This has a lasting effect on production performance. In the first year of using FASTEC 4 PRO, the OEE was increased by 5% across all lines.
The black box of the past no longer exists. The transparency of the current state of the systems alone is worth its weight in gold for us. And we’re not even talking about the various evaluation options.
Gerhard Kroker
Director Production Assembly, Dr. Willmar Schwabe Group
7 %
Eisengießerei Baumgarte: The biggest energy consumers in a foundry are the medium-frequency induction furnaces. It was therefore important for the Baumgarte iron foundry to be able to identify potential savings in this area in particular. FASTEC implemented a special monitoring view for this purpose. In addition, the department manager has the option of changing the order sequence, which by default depends on the transfer from the ERP system, directly on the production client. If unforeseen gaps occur in the upcoming production process, an energy-reducing intervention can be made immediately.
With this display, we can prepare subsequent orders perfectly. Thanks to the large monitor and the clear view, we have exactly the data we need at a glance. This has enabled us to achieve energy savings of 7% in this area alone.
Employee
Eisengiesserei Baumgarte GmbH
30 %
NORMBAU GmbH: With the help of FASTEC 4 PRO, the electricity consumption of the machines is measured in kWh via meters. The report can be made per order, per machine and per building. This data acquisition made it possible to implement optimization measures, such as the insulation of the heating belts. Significant energy savings have been achieved thanks to the data from the MES.
Other sustainability targets achieved:
- OEE increase of almost 30%
- Reduction of rejects by recognizing problem articles
- Reduction of writing effort by 90
- Identification and elimination of countless causes of errors
Sustainability plays an important role for us. In the past, we could only determine electricity consumption per building.
Thanks to FASTEC 4 PRO, we are now able to report consumption per machine and per order. This helps us to make targeted optimizations.
Christian Meier
Industrial Engineering, NORMBAU
Conclusion:
MES software solutions enable data-based store floor management, which can significantly increase resource efficiency, reduce costs and introduce more sustainable production processes. In addition, the data collected can be used to provide credible documentation.
MES are the ‘single point of truth’ across the entire value chain on the store floor. Implementing a suitable MDA/PDA solution not only provides benefits such as data acquisition and analysis for optimized and more sustainable production. MDA and PDA also form the foundation for further digitalization projects within a modular, flexibly expandable MES software solution in order to be able to grow with the requirements of digital transformation.
Implementing a software solution in an existing store floor, possibly with heterogeneous machinery, is a complex process. However, with the selection of an experienced MES partner and possible financial support, it is often less challenging than expected. Various subsidies support companies in introducing a Manufacturing Execution System (MES) to achieve sustainability goals through grants, tax breaks or funding programs.
We will be happy to advise you!
Further exciting and detailed use cases and details about the FASTEC 4 PRO solution can be found in our detailed user reports in the download portal.