The smart factory is at the centre of the digital transformation of manufacturing companies. MES software solutions control industrial production processes, collect and store data in real-time and can be used across all industries. Their modular structure makes them flexible and customisable. The software solution must constantly adapt to changing technologies, expectations and goals. Continuous further development of our software solution is therefore a matter of course.
We see ourselves as a partner to our customers and support them in various industries in the digitalisation of their production processes, often over the course of many years. For us, discussions and exchanges with our customers are therefore particularly important in order to realise the targeted further development of our software solution according to the motto “from practice – for practice!”.
Many of our customers are already experts in the use of our software solution. The longer the software is in use, the better users can evaluate and interpret the data collected and derive individual optimisation measures. Once the first or even second and third optimisation measures have been implemented, many users want to delve even deeper into the data and/or identify in practice where further functions or the recording of additional key figures might be useful for their process.
Living Customer Partnership: Incorporating Customer Experience into the Software
Several customers from various industries, with whom we have been working for many years, were no longer satisfied with the OEE indicator report alone.
The OEE figure shows the availability of machines, measured in terms of machine downtimes. However, interventions where the machines continue to run despite intervention by machine operators are not considered. From the point of view of personnel or material planning, for example, it is important to also transparently record the interventions during which the machines are not at a standstill. This is where the key figure No Touch Time (NTT) comes in. This records all interventions with and without machine downtimes. It therefore shows when the machine is running autonomously. The higher the NTT, the more autonomously the machine is running.
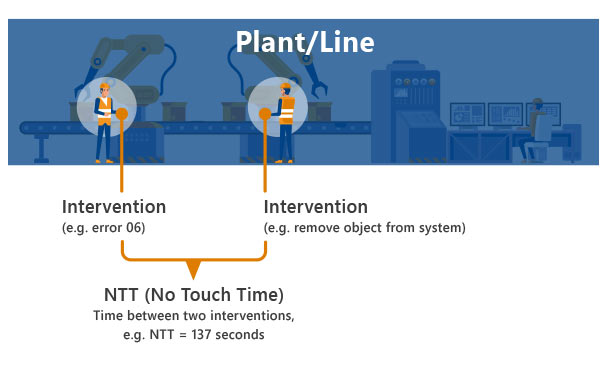
Some customers had already tested external recording systems. However, they were not satisfied with the recording and evaluation options and also wanted to avoid having to use several systems in parallel. As the key figure is relevant for many companies in different industries, we developed a corresponding solution for recording the key figure NTT, which will be made available to all customers in the standard software from March 2023 with release 3.4.4.
Best Practice-Story
A customer from the food production sector requested the integration of No Touch Time for a total of four machines. An operator intervention on these machines can be planned or unplanned, with machine downtime or without machine downtime. In this example, the company had configured 4 categories of interventions:
- Unplanned interventions without machine downtime
- Unplanned interventions with machine downtime
- Planned interventions with machine downtime
- Planned interventions without machine downtime
This example can be applied very well to many production processes. Unplanned malfunctions can be interventions where an operator takes action to avoid imminent downtime, for example by removing slipped products from the machine. Planned faults can be foil roll changes on the packaging machine, cleaning and maintenance work or quality checks.
Another request from several customers was to be able to quickly and intuitively compare the number of interventions per system or machine using a pareto report or heat map.
Implementation: Integration of the NTT Key Figure in the MDA Module
The data required to calculate the key figure is recorded in FASTEC 4 PRO via the process messages (MDA). For this purpose, a switch is installed on the machine, for example, which is pressed by the machine operator at the start and end of each operation. In addition to the – in this case – four configured categories, the duration of the intervention is also recorded in real-time.
Our formula for calculating the NTT:

In FASTEC 4 PRO, users can create NTT categories that can be individually configured and defined, for example, as planned or unplanned interventions. The desired NTT category can then be assigned to the process messages.
If a process message occurs on a machine, this is automatically recorded by the system and related to the NTT. In the NTT report of the MDA module, users can comprehensively analyse the NTT categories and respective process messages.
FASTEC 4 PRO visualises the recorded data using a pareto diagram and heat maps so that the user can quickly see when and where things got stuck. This allows our customers to derive how autonomously which machine ran and when, or which interventions took place and how long they lasted. The recorded real-time data is ultimately used to analyse and derive individual optimisation measures.
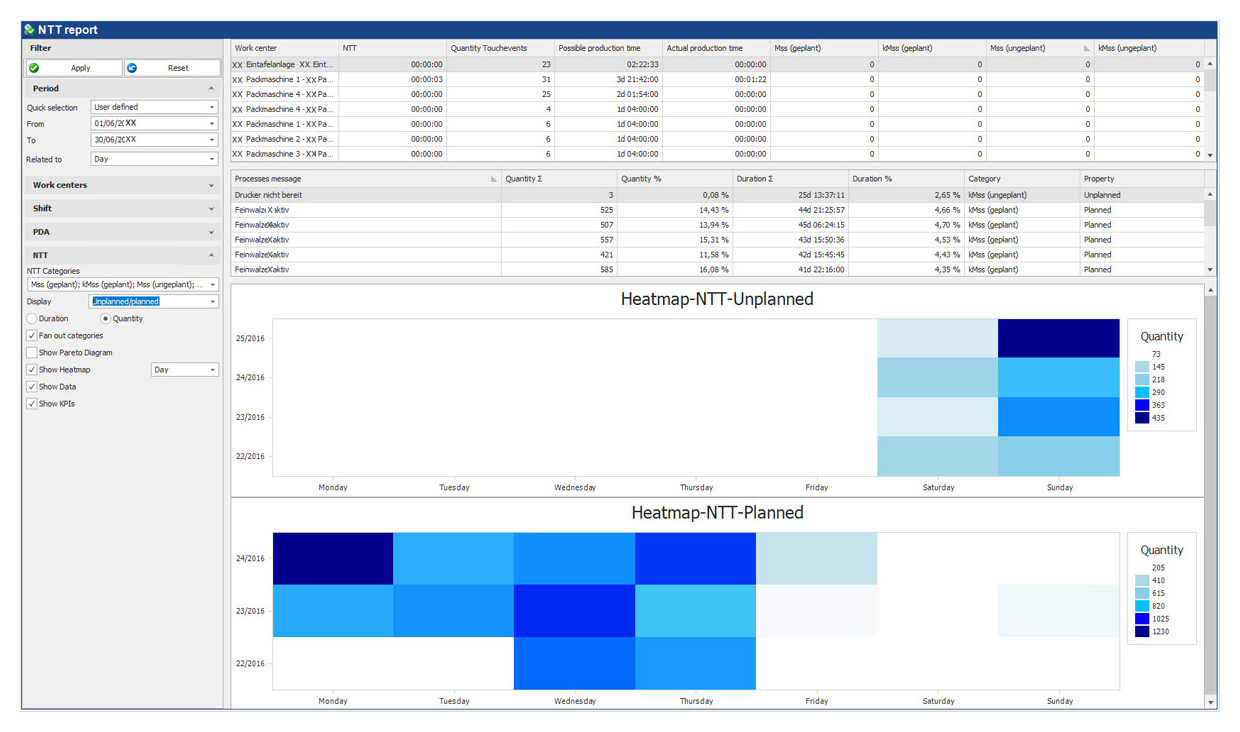
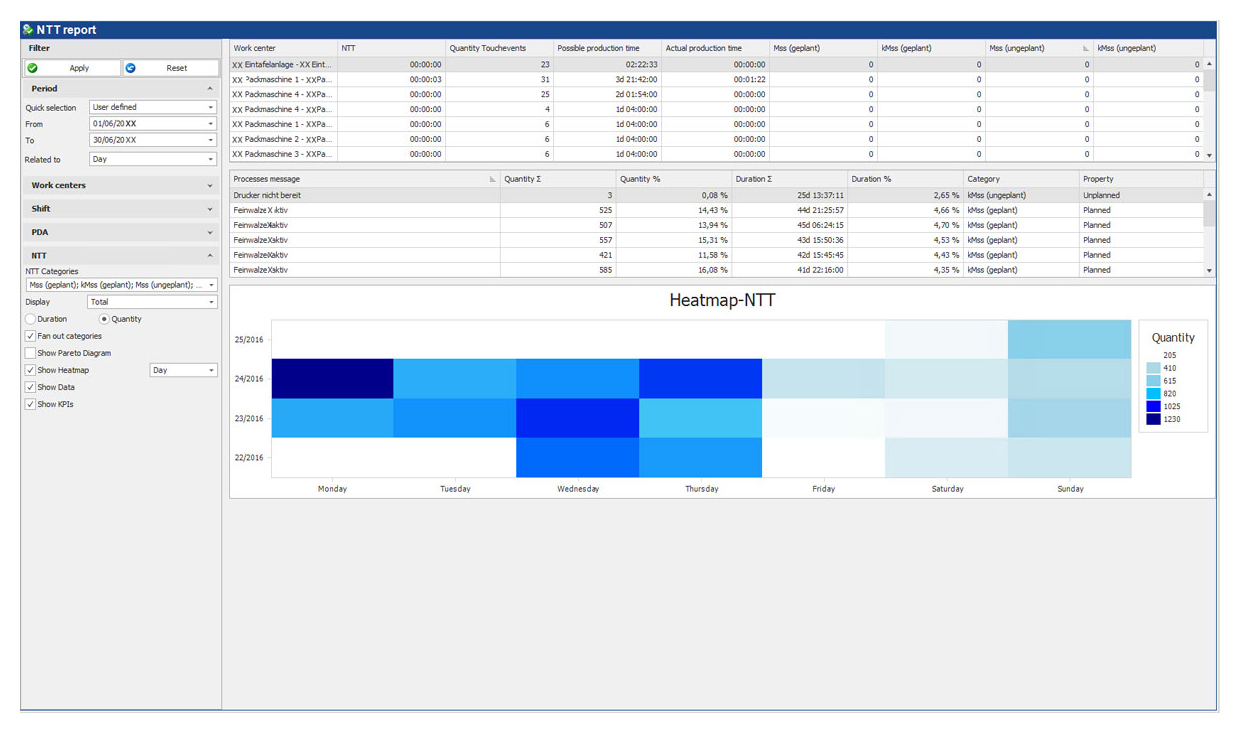
Heatmap views: differentiated reports and views possible, the darker the more frequent or longer the interventions.
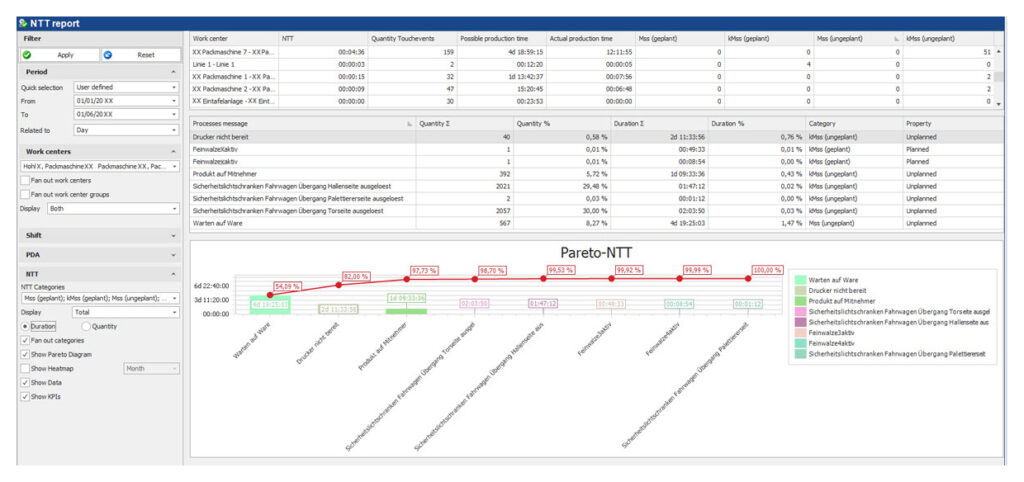
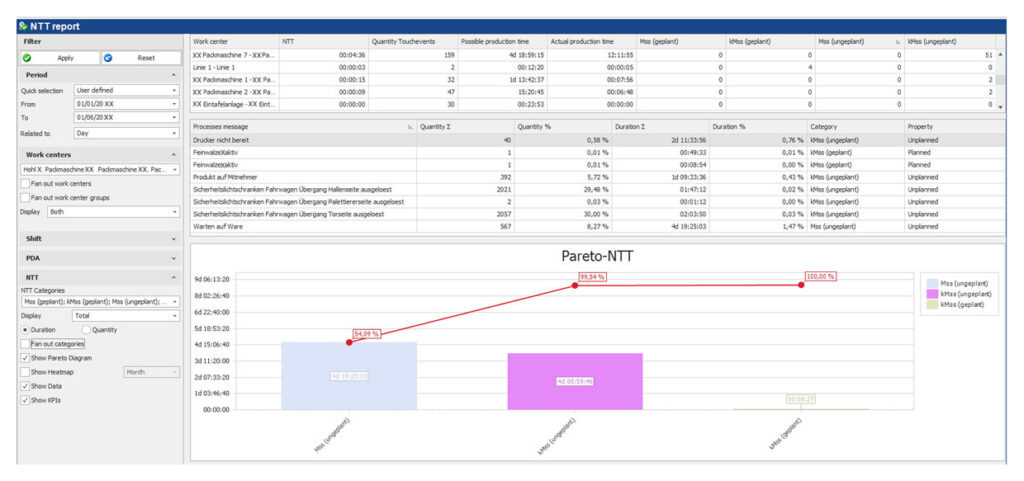
Pareto views in greater detail
This gives users an intuitive and quick overview of the number and duration of interventions on individual machines, even with a large amount of data – the darker the field, the more or longer the interventions – and they can take appropriate countermeasures.
Lively Customer Partnership
The solution was developed in response to several enquiries from customers who have been working with our FASTEC 4 PRO software solution for some time. After practical tests, we integrated it into our standard software. The result is a great benefit for all our customers – an ideal case from which everyone benefits and which we would like to repeat with further solutions. We therefore welcome feedback and dialogue with our customers. To simplify these processes, we have set up our user network FASTEC 4 YOU. However, membership is not a mandatory requirement for requests.
Our User Network FASTEC 4 YOU:
No one knows the challenges of manufacturing companies better than you do. We want our software to be better and better able to support you in overcoming these challenges. That’s why we give this user network the opportunity to have a say in potential functions and further developments in FASTEC 4 PRO and to actively participate in its development. In addition to the opportunity to submit ideas, you will be actively involved in the release process and can test new functions before they are published. We look forward to hearing from you!