Medium-sized companies are still the success factor of our economy: over 99% of all companies in Germany are SMEs. They contribute around 61% of total net value added, provide 55% of work centers and employ 80% of trainees. A real model for success – but it is faltering. Are companies still able to develop sufficient innovative strength in the digital age? What are the biggest obstacles? And which paths are already being taken successfully?
Obstacles to the Digital Transformation
In turbulent times, it is particularly important not to stick to the status quo in order to recognize the opportunities in the digital transformation for your own company and to tackle the process. Key obstacles are often:
- Obstacle 1: Unclear cost-benefit ratio: lack of transparency regarding the potential in production
- Obstacle 2: Abstract information, unclear practical relevance and lack of concept
In order to exploit the innovative power of a digital Shopfloor, it is therefore important to close the gap between knowledge or collected data and concrete action. The keys to this: Knowledge sharing, collaboration and an open mindset.
What can we offer our customers on this path? By capturing real-time data from the store floor, an MES forms the foundation for the digital transformation of manufacturing companies. The data is recorded directly at the machine or line during operation and is available in real-time for reports at all levels. That sounds good at first. However, what sounds useful and efficient is often not self-evident in practice. Once an MES software solution has been introduced, the employees in the company have to interpret the recorded data and derive their own optimization solutions from it. Other companies’ solutions can be helpful and provide a source of inspiration for your own approaches.
Solution 1: Identify optimization potential in the run-up to an investment and calculate ROI
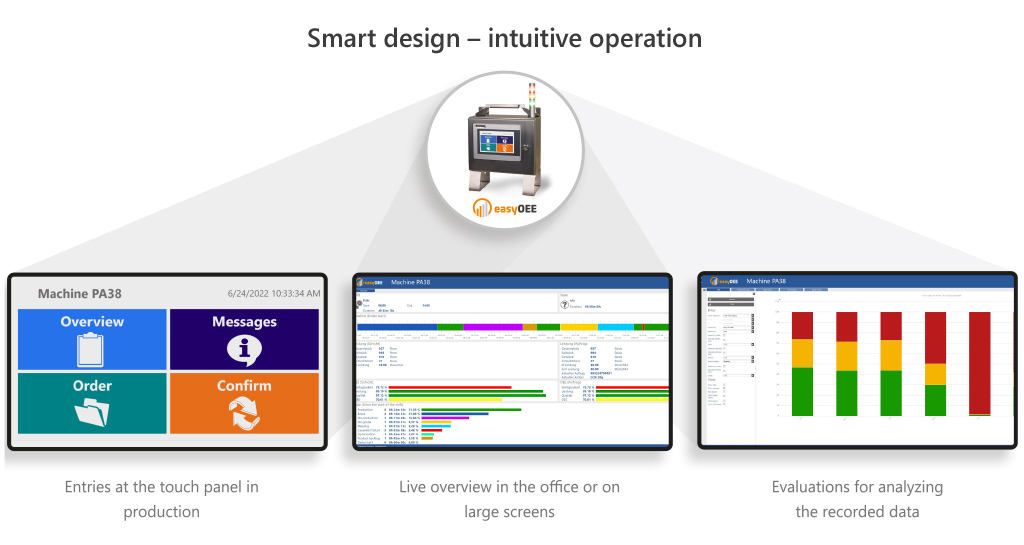
Belal Al-Shaibani, former Process Manager, MEDICE Arzneimittel Pütter GmbH & Co. KG:
We did not know the availability and performance of our lines. We therefore started with the easyOEE productivity measuring device to carry out a status quo analysis on three machines in the packaging department. Thanks to easyOEE, we were already able to increase our OEE value on these three machines by up to 11% in the first month. Building on this, the FASTEC 4 PRO MES system was then introduced, which uncovered further capacity reserves and increased OEE by another 10% in the first year of use.”
Marcus Bruns, Group IT Manager, Gustav Berning GmbH & Co. KG:
The setup of the easyOEE terminal in advance and the installation on site was successfully completed in a very short time and was almost self-explanatory. The import of the article master data from the ERP system was also possible without any problems and was carried out quickly in order to avoid parallel master data maintenance. Thanks to the additional binding of a simple hand scanner, process data such as article number and process order number are read in by the employee, thus preventing input errors. All in all, a very fast and cost-effective way to tackle and drive forward the topic of OEE in the company.”
Christopher Fischer, Plant Manager, NaBento Vliesstoff GmbH:
Exploring the potential of production and testing digital data acquisition on a system without making any major investments was the optimal solution for us. Thanks to the potential analysis with easyOEE, we knew that investing in a holistic solution was worthwhile and more economical in the long term.”
Solution 2: Diverse Solutions that Inspire – from Theory to Practice.
Customer A: A small root cause with a big impact – uncovering a cause of downtime that had lasted for years
By installing cameras on the central production lines, unplanned disruptions can be clearly identified. If the MES identifies an unplanned interruption, the complete video recording of the line activity enables the exact cause of the malfunction to be identified. This enabled our customer to identify a disruptive factor on a line that had been causing regular short downtimes and thus high costs for years.
A switch within the line was positioned slightly too far to the right, which meant that produced parts kept getting caught in it. By correcting the switch, it was possible to eliminate the cause of the malfunction and thus make the line’s production more efficient in the long term.
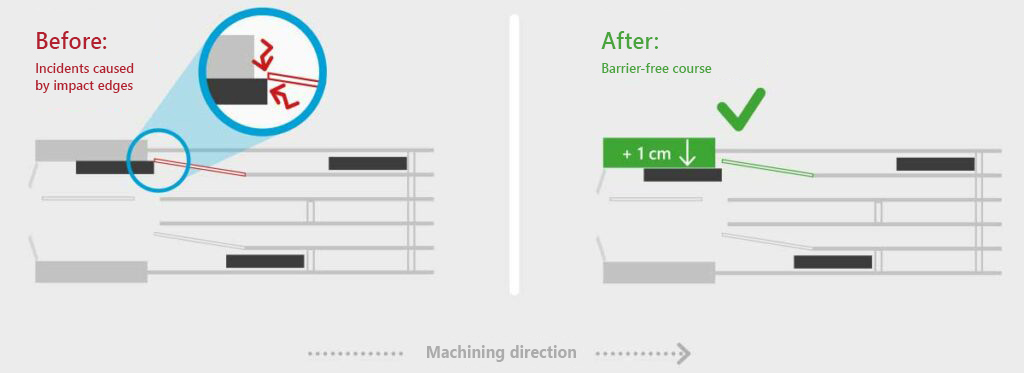
Only the real-time data recorded directly on the production lines revealed the cause of the unplanned downtime. With a small and simple correction, it was possible to rectify this permanently.
Customer B: Two birds with one stone – free repair of the system and increase in productivity
Our customer found out through digital data acquisition that the performance data on a system did not correspond to the manufacturer’s specifications. The actual productivity of the machine measured in production deviated significantly from the manufacturer’s specifications. Thanks to the transparent, digital recording of this data, it was possible to submit a complaint to the manufacturer. The manufacturer discovered that a component had been installed slightly differently to the optimum in the system setup, which led to a loss of productivity. The machine manufacturer optimized the structure free of charge, which led to the maximum cycle time of the system being achieved and thus to a considerable increase in productivity. As a result, production became significantly more efficient and customer B has since been able to save costs and achieve higher profits through increased output.
Customer C: Meeting corporate goals – sustainable production and avoiding waste through digitalization
The aspect of sustainability can also be promoted through transparent data. Our customer NORMBAU has developed best practices in this regard. Some older machines have been replaced by more productive, new machines. With the help of FASTEC 4 PRO, electricity consumption is measured in kWh via meters. The report can be made per job, per machine and per building. This data acquisition made it possible to implement optimization measures, such as insulating the heating belts. Significant energy savings have been achieved thanks to the data from the MES. This is a great success for NORMBAU.
Christian Meier, Industrial Engineering, NORMBAU:
Sustainability plays an important role for us. In the past, we could only determine electricity consumption per building. Thanks to FASTEC 4 PRO, we are now also able to report consumption per machine and per order. This helps us to make targeted optimizations.”
Customer D: Exceeding the targets set – optimization measures on the carton erector reduce short downtimes by 87.5%
The DMAIC method from Six Sigma is used to approach problems. The first step was to define the objective. A 50% reduction in short downtimes on a filling/packaging line in the small container sector. There is high production pressure on the line and the planned quantities were not achieved due to a lack of efficiency. The question arose as to which unit should be optimized in order to be able to meet the required quantities in the long term. The employees all had different opinions on this. Based on the data from FASTEC 4 PRO and a Pareto report, it quickly became clear that most productivity losses were caused by short downtimes on the carton erector. In the following steps, further reports and analyses identified various error patterns and uncovered the root causes. For example, it was noticed that the cartons were sticking together more frequently as the pressure roller sporadically got stuck. Furthermore, excessive humidity in production led to instability of the cartons, which meant that the stacker could not work cleanly and cartons were occasionally crushed in the production process. Through various optimization measures, such as repairing the inserts of the pressure roller and redesigning the stacker, high efficiency potentials were activated and the target set at the input was far exceeded. Short downtimes on the system were reduced by 87.5 % thanks to the optimization measures on the carton erector.
Conclusion:
The hurdle to taking the first step towards digital production still seems high for the majority of SMEs. Decision-makers are faced with two key obstacles: the expected results are often not tangible and there is a lack of concrete examples of how digital software solutions can help optimize production and increase efficiency.
With our potential analysis, we help you to uncover the potential in your production in a flexible and uncomplicated way. This will tell you whether investing in an MES is worthwhile in the long term. Take a look at the best practices of our customers in our user reports and see specific use cases of the MES solution for yourself.
Even limited internal know-how for the implementation of digitalization projects should not stand in the way of the project. We see ourselves as a customer partner and support our customers from consulting to far beyond the implementation of the software solution. During implementation, a good network of stakeholders is needed so that you do not face change alone, but can draw on the experience of others. We accompany our customers from various industries on this path. Since 1995.