User Report Dalli-Werke GmbH & Co. KG
The FASTEC 4 PRO software solution at WIN AEROSOL GmbH & Co. KG, a subsidiary of DALLI-WERKE GmbH & Co. KG.
The full report is available for download.
The FASTEC 4 PRO Software Solution at Dalli-Werke GmbH & Co. KG
The dalli group is a sixth-generation family business with a clear focus on the European private label and brand business. In line with its promise of quality, the medium-sized company combines tradition, values and social responsibility with the demands of a high-performance and future-oriented group of companies – and has been doing so for over 175 years.
At WIN AEROSOL GmbH & Co. KG, a subsidiary of DALLI-WERKE GmbH & Co. KG, FASTEC 4 PRO has been introduced on all lines in order to reduce the manual effort involved in data acquisition and its analysis and archiving in reports. Thanks to digital data acquisition, the production manager now saves eight hours a week, which he can devote to other tasks.
- Modules Used:
– Machine data acquisition (MDA)
– Production data acquisition (PDA)
– and the Additional Function View Client - Special Features:
– All data is recorded via I/O modules on the lines.
– Central key figure: pieces per shift
– Each product is calculated and a calculated price is passed on to the customer with a margin.
– In order to produce the products at the calculated quantities, a cycle per minute, i.e. a number of pieces per minute, is required. Production is measured by this key figure.
– Strong focus on cost savings, less on OEE
“We found out things that we didn't know before. I didn't realize how much potential there was to increase output by just a few minutes during shift changes. We only became aware of this thanks to the documented downtimes.”
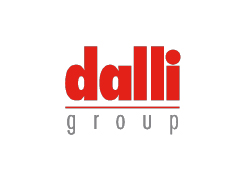
"The biggest benefit is that I can call up various key figures with just a few clicks."
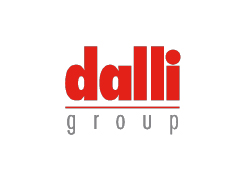
"The user interface in the Office Client is very intuitive, and the online help offers extensive information on a wide range of scenarios. It meets all my requirements and I get on very well with it."
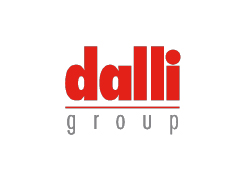
"We had very good support from FASTEC right from the start. We also attended the user forum in Paderborn and were able to hear first-hand experiences from other users and exchange ideas, which was very convincing and very helpful!"
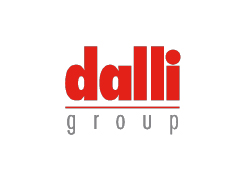
Short and Precise
Facts Instead of Gut Feeling:
Without a transparent database, it is almost impossible to uncover potential in production. At WIN AEROSOL, too, potentials for the output quantity came to light that were previously unknown. Several minutes were regularly wasted during shift changes, which would have meant enormous increases in productivity with more efficient processes.
The recording of downtimes was also adapted over time. Initially, five minutes of production downtime were tolerated until an unjustified fault was triggered in the system. Today, we go much deeper in order to record downtimes more accurately. This allows a clear lever to be identified in the loss of performance and downtimes can be better assigned to their origin.
Transparency Across All Departments:
Large screens can be found throughout the site, showing a dashboard from FASTEC 4 PRO. Production, production control, technology, logistics and quality management can see the current status of all lines and when an order has been completed. In addition, employees in the office have the option of carrying out reports on KPIs at any time. All information can be called up in real-time at the touch of a button and then serves as a basis for meetings, for example.
Result: Eight Hours/Week Of Time Saved:
The production manager spent almost two hours a day collecting, analyzing and archiving data from the production lines. Further hours were added for the weekly and monthly analyses. Time that is very valuable as a production manager and can be better invested in other activities.
This time saving through digital data acquisition with FASTEC 4 PRO is the biggest lever at WIN AEROSOL: the production manager saves eight hours a week!
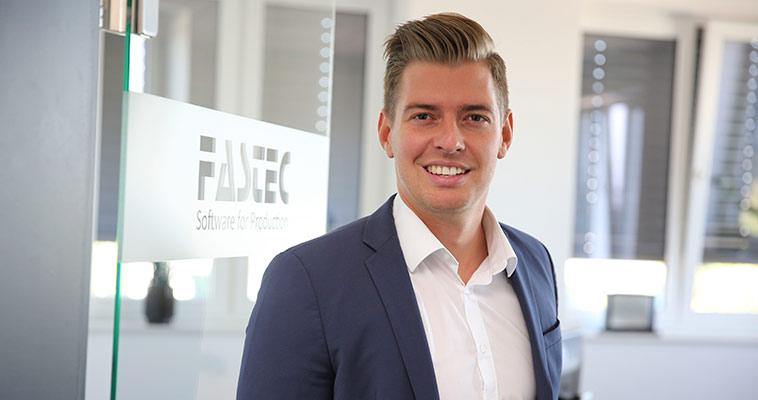
Do You Have Special Requirements for Digital Production Management?
No problem. We deliver customized solutions. With us, you benefit from extensive project experience in digital manufacturing in various industries. With over 400 customers. Worldwide. Since 1995.
Who We Work For
From automotive suppliers to food producers, pharmaceutical companies to toy manufacturers, from highly specialized niche suppliers to ambitious medium-sized companies to large international corporations – over 400 customers around the globe rely on Software for Production – made in Paderborn. Among them:
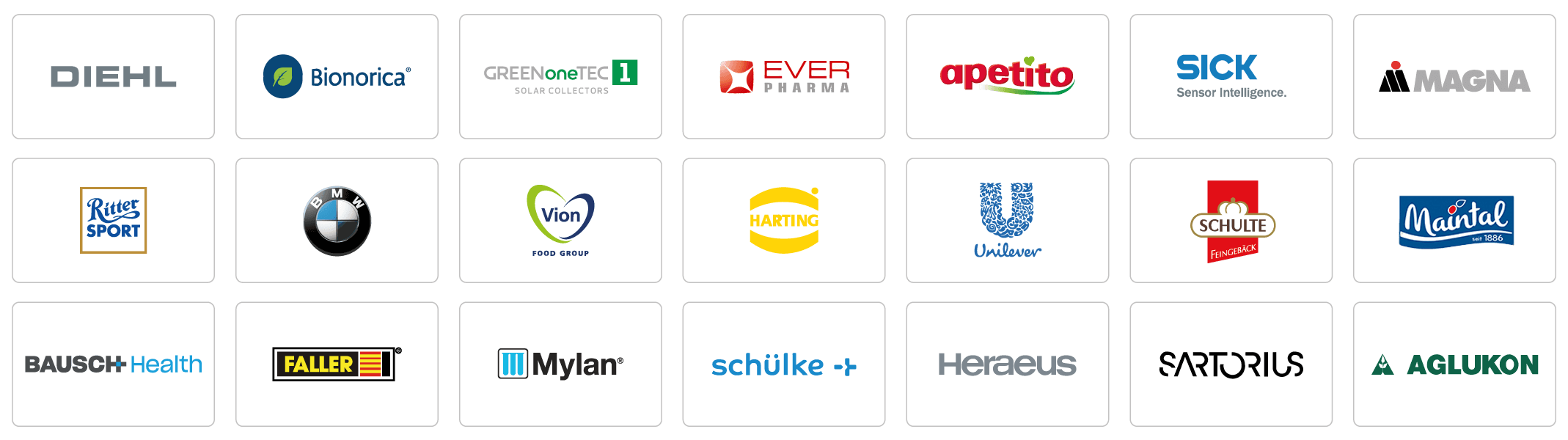
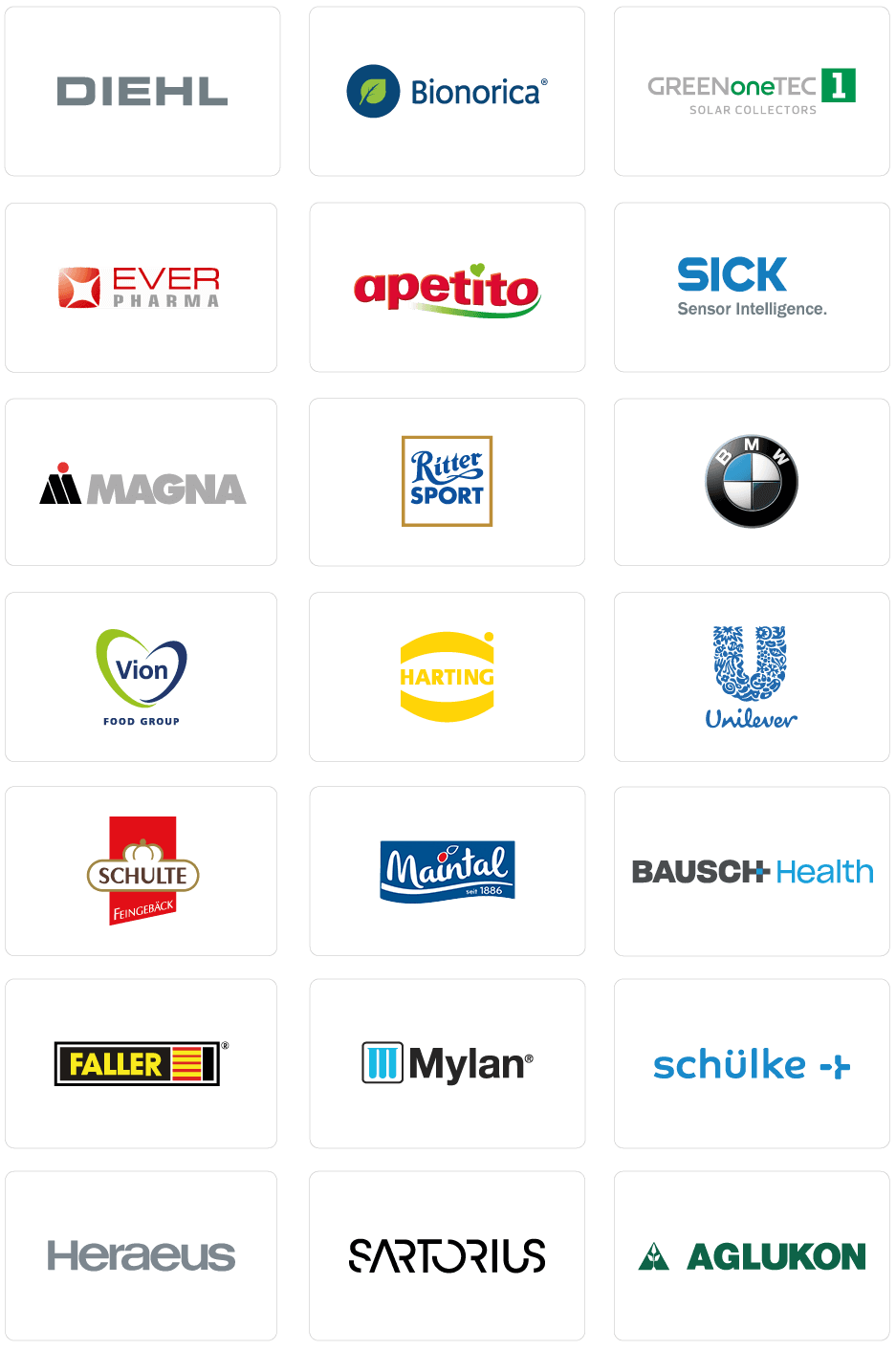