User Report: Diehl Controls
MES solution FASTEC 4 PRO at Diehl Controls, Wangen site.
The full report is available for download.
The FASTEC 4 PRO Software Solution at Diehl Controls
Among industrial companies, the competition for the “Factory of the Year/Global Excellence in Operations” award is considered one of the toughest benchmark competitions in Europe. The overall winner in 2015 was Diehl Controls in Wangen. The company impressed the jury with its transparent and fully automated production line. The MES FASTEC 4 PRO made a decisive contribution to this success.
Diehl Controls is one of the world’s leading manufacturers of electronic components for the household appliance industry (appliances) and hardware and software as well as backend solutions for intelligent energy management systems in buildings.
- Industry: Electronics
- In Use: MES solution FASTEC 4 PRO with the Machine Data Acquisition module and the Additional Functions Monitoring, Process Data Acquisition and Process Messages
- Interfaces: To SAP-BW and FIT system (FIT = Functional Integration Tester)
- Connected Systems: 7 speed lines, 1 test and assembly line,
3 SMT lines
“At the beginning, we didn't use the FASTEC system as intensively as we do today – partly because we weren't yet aware of the potential of FASTEC. Depending on the product, we have now achieved an OEE increase of 5-15%.”
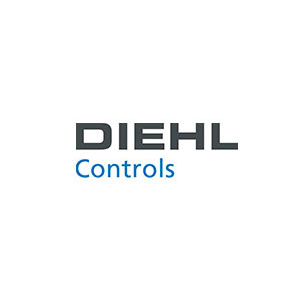
Short and Precise
Factory of the Year 2015 with Transparent, Fully Automated Production Lines
In addition to its business activities in the appliance sector, Diehl Controls has also accommodated Connectivity Solutions at its site in Wangen. The plant’s machinery now comprises seven speed lines – the largest of which, with a length of 86 meters, now consists of 73 modules. There is also a test and assembly line and three SMT lines.
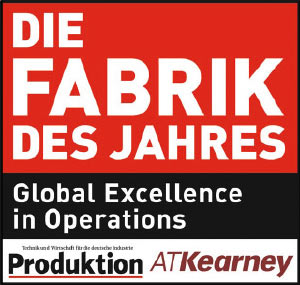
Decision in Favor of FASTEC Due to the High Flexibility of the MES
The go-ahead for the introduction of an MES system at Diehl Controls in Wangen was given in 2009. Until then, the company had been using the self-developed system “My MDA” to bring transparency to the production process through monitoring. Due to the high costs and manpower required to operate the system, the management board decided to replace “My MDA” with a commercial MES system. The main reason for choosing FASTEC was the high flexibility of FASTEC 4 PRO – a decision that proved to be the right one against the background of the further development of Diehl Controls in Wangen.
Lean Management in Its Purest Form
The corporate philosophy of Diehl Controls is characterized by transparency, common goals and fairness towards the individual employees. Information and communication are essential prerequisites for this. A term that has gained in importance both in this context and in connection with Industry 4.0 is store floor management: the presentation of production-relevant information, tailored to the respective target group, in the middle of production plays a central role in this.
Monitoring in Almost Every Department
Stefan Wespel reports: “At the beginning, we didn’t use the FASTEC system as intensively as we do today – partly because we weren’t yet aware of the potential of FASTEC. Our efforts to continue developing our production in the direction of Industry 4.0 led us to take a close look at this tool. We have used it to make production more transparent and the preparation of data easier and more comprehensible for everyone, so that everyone can work with it without any problems. The system has paid off for us, especially in recent years, because we can use it in a large number of departments and adapt it flexibly to the requirements of the departments. Monitoring has become indispensable for our production today.”
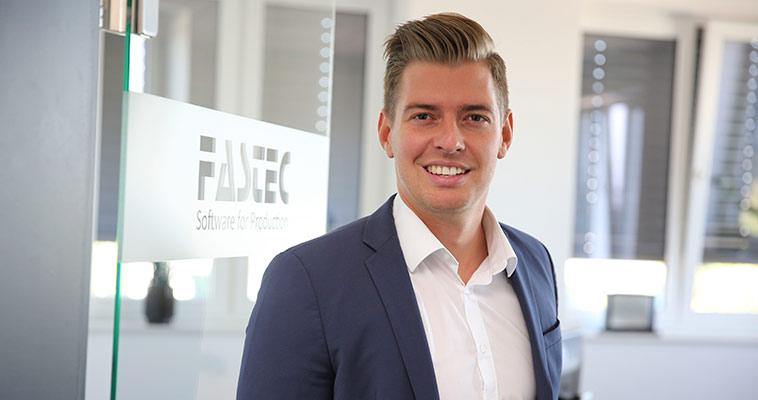
Do You Have Special Requirements for Digital Production Management?
No problem. We deliver customized solutions. With us, you benefit from extensive project experience in digital manufacturing in various industries. With over 400 customers. Worldwide. Since 1995.
Who We Work For
From automotive suppliers to food producers, pharmaceutical companies to toy manufacturers, from highly specialized niche suppliers to ambitious medium-sized companies to large international corporations – over 400 customers around the globe rely on Software for Production – made in Paderborn. Among them:
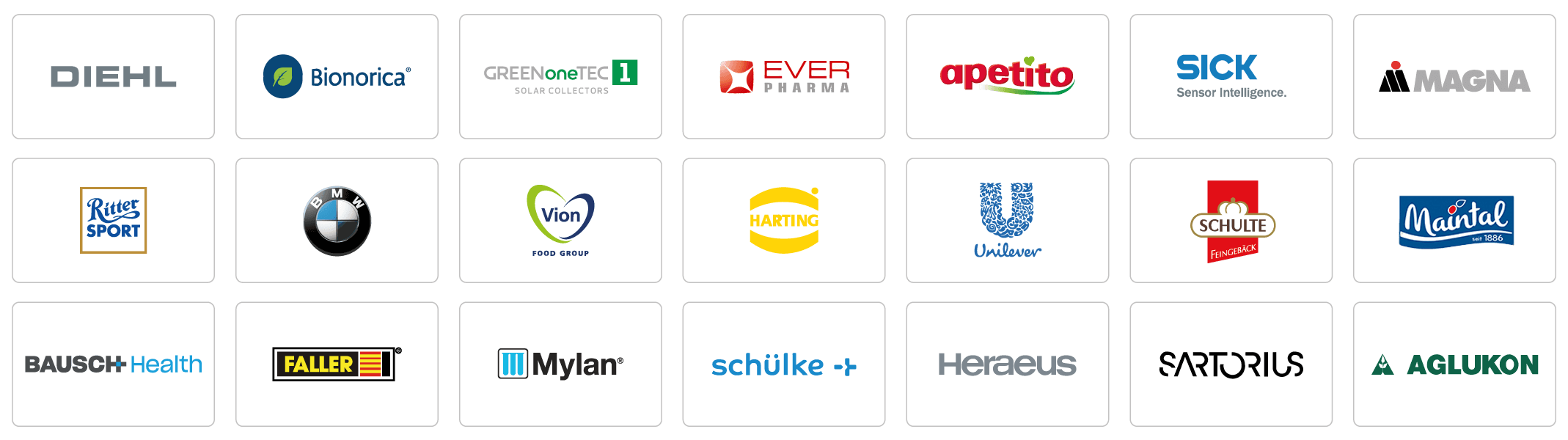
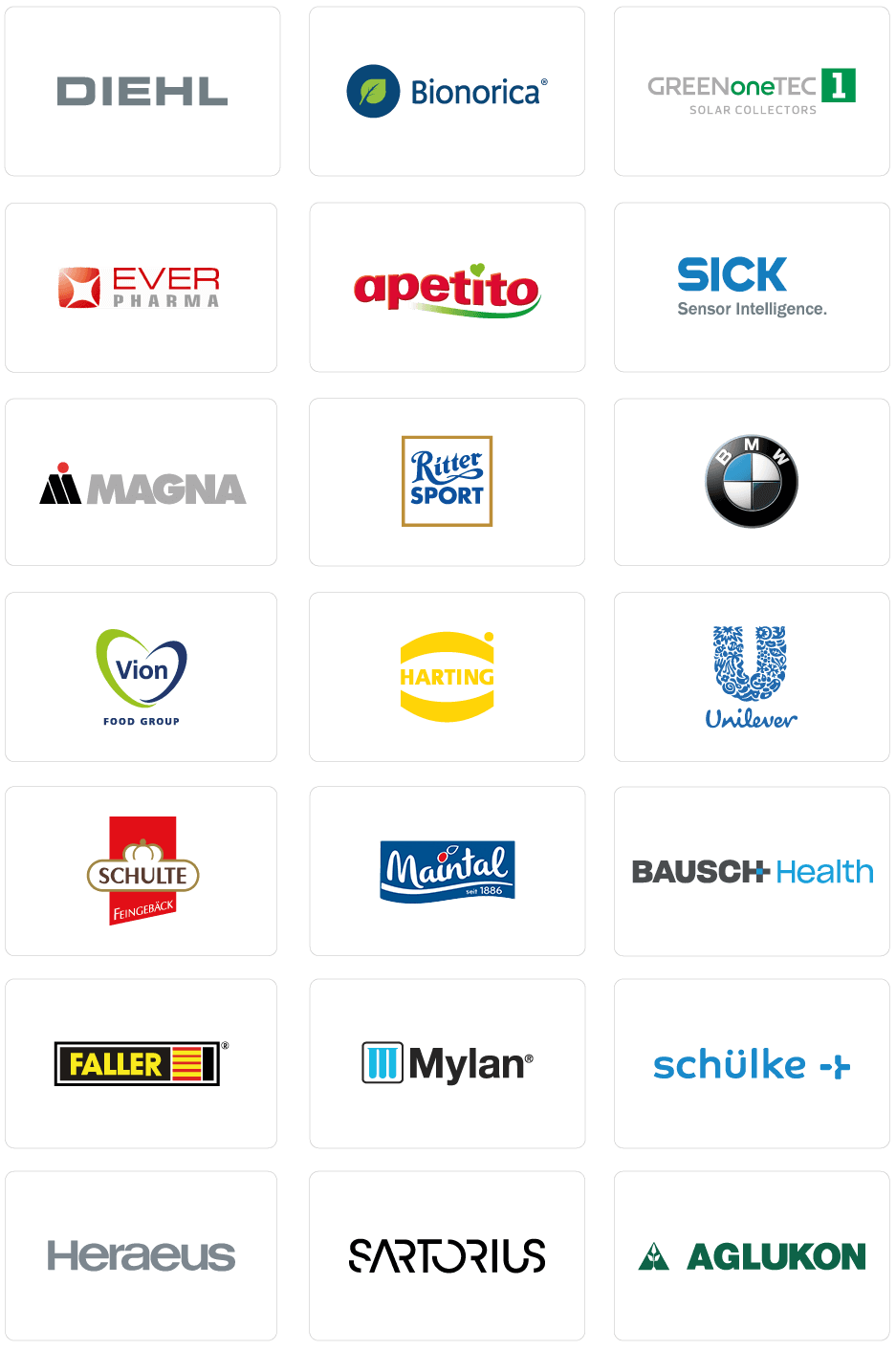