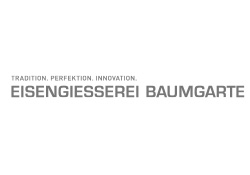
The introduction of a modern MES system enables the Baumgarte iron foundry to respond to increasing customer requirements for cast parts and to keep costs as low as possible.
As one of the largest German foundries with three moulding plants and a wide range of references in very different sectors, Eisengiesserei Baumgarte has stood for sophisticated, modern casting technology, top quality and pioneering technology for many decades. Baumgarte currently employs 230 people on a production area of around 20,000 square metres, who cast and process around 30,000 tonnes of cast parts per year in state-of-the-art production facilities.
Baumgarte keeps an eye on the changing market conditions, constantly adapts its manufacturing and production technology to the times and develops processes in the technical and administrative areas. The introduction of an MES system was an important step towards the future.
Volker Spruch, Head of Technical Controlling at Eisengießerei Baumgarte, also recognised this necessity: “With an MES system, we can react to changing market conditions and implement the increasing customer requirements for cast parts while maintaining consistently high quality. An MES system also provides us with up-to-date performance and cost data at all times.”
At the end of 2010, the go-ahead was given for the introduction of the FASTEC 4 PRO MES system from the Paderborn-based software company FASTEC. The Machine Data Acquisition (MDA) module was implemented as a pilot installation on two core shooting systems. This MDA module was put into operation quickly and easily thanks to the requirements for the MES system that had been worked out in advance. Just six months after the pilot installation, the system was extended to the remaining twelve machines in the core shop in spring 2011. In August of the same year, a total of three moulding lines followed. Two of the moulding lines were connected “classically” via FASTEC 1/0 modules, while one moulding line was bound via a special XML-based web interface.
The next step in the project was to realise an interface to the existing ERP system so that the ERP and MES systems could communicate with each other. Baumgarte uses the Guss info ERP system from sd software, which was specially developed for foundries and the metalworking industry.
Interface Solution Based on XML
The interface for transferring orders from the ERP system was the centrepiece of this project step. In contrast to the core shooters already implemented, various orders can be produced in one moulding box with the integrated moulding systems.
In order to transfer these orders from the ERP system to the MES system, a complex and sophisticated XML-based interface solution was realised. All orders for the moulding plant are combined and an “overorder” is created. This transfer order can then be logged in and out of the MES system in the same way as the regular orders.
To visualise the whole process, a special monitoring view was created for the production terminals on the moulding lines. Here, the department manager can see the overorder with the relevant data in the upper area and all sub-orders with target quantity, 10 and NOK quantity, part number, etc. directly below. Once the transfer order has been completed, i.e. when the specified target quantity has been reached and the machine operator has reported the order as “completed” in FASTEC 4 PRO, detailed order feedback is sent to the ERP system, including states, times and counter readings. This detailed data transfer enables an exact recalculation of the orders directly in the ERP system: machine and setup times, downtimes as well as good and scrap quantities are recorded precisely in the MES system and made available to the SD system in the appropriate format.
Those responsible at the Baumgarte iron foundry were convinced by the possibilities of the interface solution originally implemented for the moulding plants, so that all machines were realised via the SO interface. Volker Spruch summarises this: “Thanks to our special SO interface to our ERP system, we are now able to recalculate orders in detail.”
Work Less Error-Prone with MES
For easier, paperless working, Baumgarte also licenced the MES module Document Display. “As we already use Windream, a programme for electronic document management, in our company, we also needed an interface between FASTEC 4 PRO and Windream,” comments Volker Spruch on the requirements for the FASTEC solution.
At Baumgarte, the link to Windream was then realised as follows: When the machine operator registers an order at the production terminal, a storage location in Windream is automatically transmitted with the order data so that the MES system can immediately apply the current files with the registered order. This means that all relevant documents are displayed to the employee on the terminal when they log on to the order, such as work instructions, set-up information, processing instructions, etc. For the Baumgarte iron foundry, this procedure offers the advantage that up-to-date documents are always available directly at the required work location or terminal. Another advantage is that this link avoids duplicate data storage.
The largest energy consumers in a foundry are the medium-frequency induction furnaces. It was therefore important for the Baumgarte iron foundry to be able to identify potential savings in this area in particular. FASTEC realised a special monitoring view for this purpose. The current states of the systems and the next orders to be processed are displayed to the employees on a large screen directly at the control centre of the furnaces. The order data for this is applied directly from the ERP system via the SO interface.
The melting furnace view shows the order number, item, customer, temperatures, materials, weight and moulding plant malfunction or downtime at a glance. This allows employees to make the necessary preparations for set-up, weigh the input material and make it available. The department manager also has the option of changing the order sequence transmitted from the ERP system directly on the production client. If unforeseen gaps occur in the upcoming production sequence, an energy-reducing intervention can be made immediately.
The employees in the department are delighted with the furnace view, as Volker Spruch reports: “With this view, we can prepare subsequent orders perfectly. Thanks to the large monitor and the clear view, we have exactly the data we need at a glance. This has enabled us to achieve energy savings of around seven per cent in this area alone.”
Equipped for the Future
Step by step, all areas of production were integrated into the MES system. For example, six machining centres and seven special core shooters were integrated at the beginning of 2013. A new machining centre for processing pump housings was commissioned in 2014. “Thanks to the simple configuration of FASTEC 4 PRO, we can integrate new machines and systems into the system quickly and easily,” confirms Volker Spruch.
Eckhard Winter, one of the Managing Directors of Eisengießerei Baumgarte, is also convinced of the benefits of the MES system: ,,The bottom line is that with FASTEC 4 PRO we have immediately usable data available to us in real-time, which we can use to carry out an audit at any time within five minutes. With our MES system, we are equipped for the future and able to maintain our position in the highly competitive foundry market.”