Optimized processes, flexible responses, real-time data – the smart factory is at the heart of the digital transformation of manufacturing companies. The challenges are enormous. In addition to developing new products or investing in future-proof technologies, digitalized production in particular plays a key role in securing long-term competitiveness in order to be fit for the future.
Companies with a high degree of digitalization are in a better position, and not just in pandemic times. Even during the financial and economic crisis of 2008/2009, highly digitalized companies had a clear advantage, as a study by ZEW Mannheim shows. Productivity levels and growth remained almost constant at these companies. In contrast, they fell sharply at less digitized companies. The digital pioneers were also more likely to be able to react flexibly, implement process innovations or cut costs. They were more resilient.
But in many industrial companies, the situation is still very different. Historically grown IT island solutions cause data chaos in production. As a result, these companies cannot react flexibly enough to disruptions such as short-term order changes in the production process despite using IT applications. As a result, they often still rely on in-house developed systems or Excel and paper documentation for their operational planning. As a result, production processes cannot be planned, executed or tracked efficiently. Flexible adjustments to events – for example in planning – are not possible or only possible with great effort and with a time delay. Feedback to the ERP system is then often only provided once per shift or at the end of an order. This means that no spontaneous answers can be given to questions that are important for day-to-day business. Smart/intelligent production seems unattainable.
In the past, manufacturing companies with a smaller number of variants and less automation were able to manage detailed scheduling manually and rely on the many years of experience of their employees. Due to today’s abundance of data and complexity, this is no longer possible.
The Road to the Smart Factory Still Seems Long for Many Companies.
The vision: an intelligent factory with networked resources and systems. Every machine knows its orders, components communicate with each other about their destinations. The product finds its way through the store floor to finally reach the customer directly – that is the idea. Even if some companies are already coming close to this ideal with model factories, it is questionable whether and when this ideal will and must become the norm for German factories.
What is certain, however, is that manufacturing companies need to make their production more flexible, sustainable and responsive.
The more transparently complex processes are recorded, the faster and better companies can react to disruptions or changes in external conditions.
The Contribution of the MES – Capturing and Integrating Relevant Information in Real-Time
A Manufacturing Execution System (MES) is a system in operational production management and provides support for tasks such as production planning and Control. The main tasks of MES include, for example, Detailed Scheduling, Quality Assurance or Maintenance. The MES provides a digital image of production and enables real-time monitoring of production processes
Thanks to the ability to collect extensive and diverse data, the MES forms a data hub that enables horizontal integration. Real-time information on orders and resources is recorded, processed and stored in the MES via operational and Machine Data Acquisition – in normal/regular operation, but also in the event of malfunctions.
In addition to horizontal integration, the MES also enables vertical integration. MESs are therefore the link between the ERP system and the machine and execution level of the production process. This creates continuous transparency about current and pending orders and resource statuses.
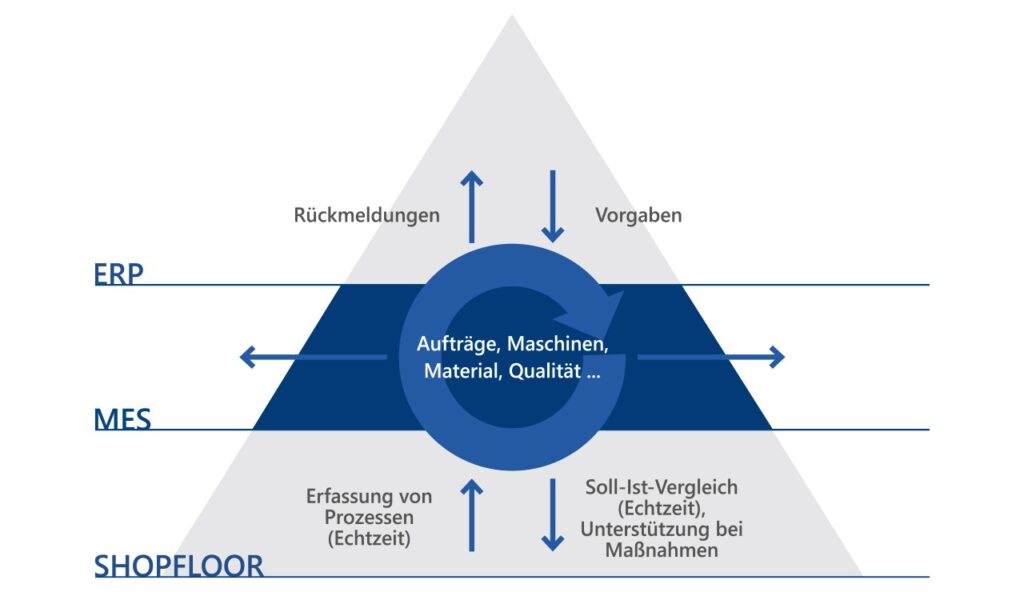
MES as a data hub between ERP and shopfloor level (horizontally and vertically integrated)
MES are multifunctional applications that are to be understood as a fusion of many, partly individual systems, which were previously often realized as isolated solutions. The data collected digitally and systematically by the MES can be used to uncover weak points, support employees, design continuous information flows, react with foresight and improve processes in the long term.
Transparent data in real-time forms the basis for combining questions about production efficiency or capacity utilization with the technical capabilities of the production facilities. Only then are fact-based decisions possible in order to optimize existing processes and actively shape the future of production in the company.
MES as an Important Step towards the Smart Factory
With an MES, data is available at every location in production and can be linked together for all processes. As the central information system in the plant, the rollout of an MES therefore plays a key role in the digital transformation. MES lays the foundation on the path to Industry 4.0, AI, machine learning, digital twins, cloud, digitalization and IIoT. All of these technologies contribute to the larger goal of the smart factory. However, this can only be achieved step by step – individually and with a strategic roadmap.
However, the increased responsiveness and the resulting flexibility are also reflected in advance; monetarily in an increase in machine and system efficiency, a reduction in throughput times and inventories or an increase in process reliability and relief for employees.