What Data Is Needed?
High-quality data is required for AI, machine learning or deep learning projects to be successful. To enable AI learning, the database used should be as extensive as possible. However, this ideal situation does not always exist in practice.
BI tools and data analyses can be used to analyze past scenarios based on this data in order to identify sources of error and implement future improvements. To do this, manufacturing companies need to collect extensive data at the machines and lines during production and store it over a longer period of time.
At this point, the question arises as to where this data is stored. Flexible scalability, cost savings and simple administration compared to an on-premises solution speak in favor of using the cloud. On-site, there are generally insufficient IT resources available for these data volumes. In the cloud, these are available indefinitely and can be used as required, which reduces costs.
Regardless of the storage solution, predictions can be made about future events based on historical data. These are based on certain constellations of parameters that are individual to each company (e.g. settings on machines or lines in production). For example, the AI learns that more rejects were produced in the past with specific process parameters and can then issue warnings in real-time if a process is highly likely to be running in a suboptimal setup.
It is therefore not only the pure quantity that is relevant, but in particular real-time data and stored “historical” data. And this is where MES software solutions such as FASTEC 4 PRO come into play.
The Data Source Is Crucial!
MES are the ideal gateway for high-quality data from production!
Manufacturing Execution Systems (MES) with modules for Machine Data Acquisition (MDA) and Production Data Acquisition (PDA) are an ideal tool for collecting relevant, accurate and high-quality data in production. If the software provider also has a high level of interface expertise and experience in binding heterogeneous machine parks, nothing stands in the way of collecting high-quality and comprehensive data directly from production. Traditionally, the data collected via the MES is stored and reported locally. However, in order to develop AI solutions or use BI tools, the data must be available in the cloud and collected there. The MES thus becomes the gateway to the cloud.
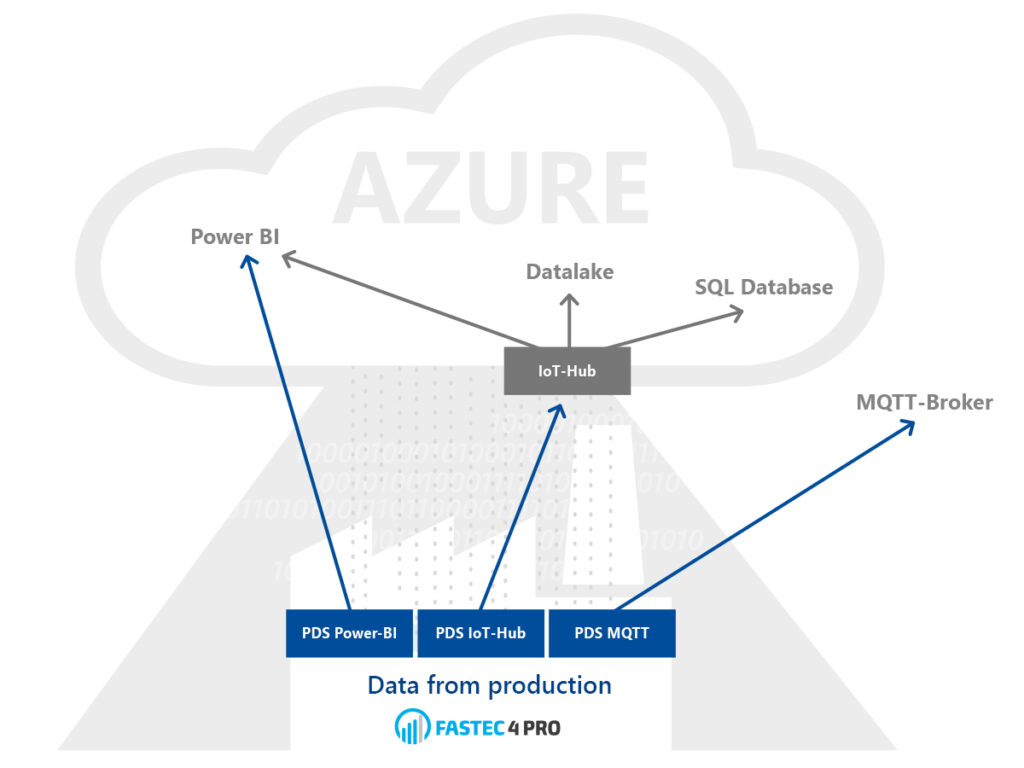
Where Is the Data Moved To?
In the cloud, for example, multiple services are available to users via Microsoft Azure. In addition to the services that Microsoft offers via the Azure portal, a number of third-party providers make software available directly via Azure. So a lot is possible in the Azure world.
The Push Dataset Streaming (PDS) jobs in FASTEC 4 PRO can be used to define directly and very easily to which service the data should be pushed.
Best Practice Examples:
1) Controlling Processes and Optimizing Machine Settings with AI Using the Example of “Manufacturing Microtechnical Products”
A company in the development and manufacture of microtechnical products uses an injection molding machine to produce plastic parts in large quantities and at high speed, which are then automatically tested for quality and product properties on a testing machine.
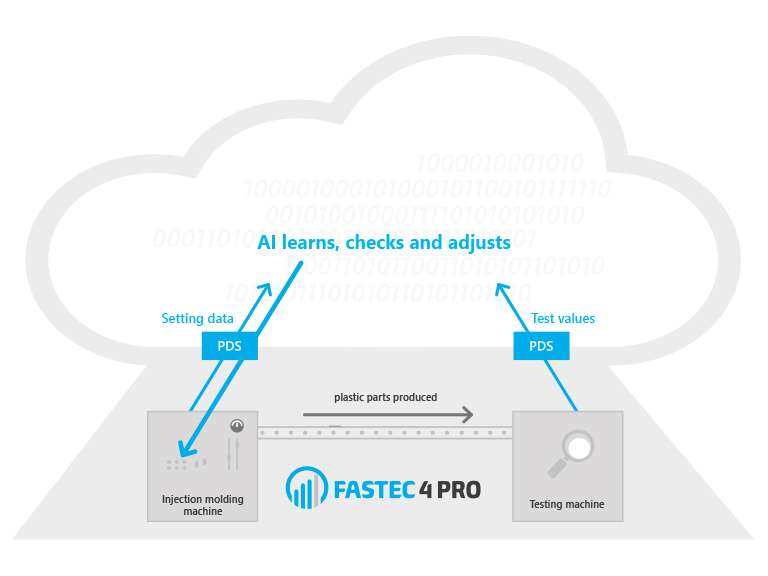
To make this process more efficient, a machine learning project was developed in collaboration with the service provider paiqo. The settings and process data recorded on the machine in FASTEC 4 PRO are pushed to the cloud in real-time for each part produced via the FASTEC Cloud Connector. At almost the same time, the automatic testing machine also sends the test results from the QA module in FASTEC 4 PRO to the cloud via the FASTEC Cloud Connector, so that process data and test data are available. The artificial intelligence (AI) in the cloud compares this data with each other. Machine learning (ML) is used to develop individual parameters according to the respective process in order to influence the settings of the producing machine. These are continuously readjusted and fine-tuned based on the results from the AI. The data from the automatic testing machine is used to directly compare whether the new settings improve or otherwise change the quality of the products. Based on these results, the settings of the producing machine are automatically further optimized. Each part produced leads to a better setting of the producing machine and, in the best case, is a little bit better than its predecessor.
2) Classification and Packaging of Products with AI Using the Example of “Bündnerfleisch”
Bündnerfleisch is a specialty made from beef from the Swiss canton of Graubünden. This high-priced product is subject to strict quality criteria, which must be checked before the packaging process in production. For a long time, this inspection was carried out manually at the company. One employee walked up and down the line and only had a fragmented view of the packaging process due to time constraints. This led to product recalls because products of inferior quality (fat content in Bündnerfleisch was above the target value) were released into the market.
In production, the products are assigned to quality criteria from quality A to D. For exclusive customers with a high-priced range, only quality A and B are sold; C and D are sorted out and processed into other products, such as salami, and sold at a lower price.
The manual allocation of quality criteria is very time-consuming and error-prone. This is the ideal environment for a process change using an AI solution. This is implemented using a camera that captures the product. Based on the captured image data, the AI decides how each individual product is categorized and with which quality criterion it is subsequently packaged.
Only around 200 images were required for this process, which were initially assigned to the quality criteria in order to train the AI. Based on this, AI models could be retrained to imitate human behavior with 98% certainty.
1.) Employee checks quality and classifies manually
2.) The data captured by the camera data is categorized.
3) AI classifies and controls sorting, employee controls
3) Predictive Quality with AI Using the Example of a Food Line “Hash Browns”
In the food production process, precise compliance with production steps and product characteristics is often essential. In addition, complex lines are often used.
Several successive process steps result in the phenomenon that settings at the beginning of the line have an impact on the quality of the end product at a later stage. For example, if a dough is stirred at the beginning of the line, stirring it too long or too short can affect the properties, e.g. the consistency of the mixture. This deviation can have a detrimental effect in the subsequent steps. This results in more rejects.
One of our customers processes batches of potatoes that are delivered directly from the field by various farmers. As a natural product, the potatoes have different qualities in terms of starch content, moisture content, size, shape and other characteristics. The first step involves processing steps such as washing, sorting and peeling. The vegetables are then processed into a basic mass for hash browns in batches. The characteristics of the potatoes are reflected in the base mass. These influence the setting parameters of the systems.
Example: How should the hash browns ideally be deep-fried to ensure that sufficient moisture content is retained in the finished product and that the product quality of the article for sale is consistent? One rejection criterion, for example, is underweight due to insufficient water content. Based on the measured values at the start of the line, the AI can control the throughput time at the fryer and use machine learning to adjust the process values ideally and in real-time
4) Steps for Successful Implementation
Find Experienced Partners:
Digitalization and AI projects are a continuous process that involves working with sensitive data, among other things. Continuous and trusting collaboration with experienced technology partners is therefore the basis for the success of these projects.
Collect Data (in the Cloud) at an Early Stage:
A solid foundation of digitally recorded production data is a prerequisite for future AI projects. Therefore, start collecting high-quality data at an early stage so that you have sufficient historical data of the appropriate quality available for later or already planned AI projects. We support you on this path with our FASTEC 4 PRO software solution!
Start with a Pilot Project in a Test Environment:
With a pilot project, the technology can be tested in a test environment without risk and thus the potential for applications and tasks can be analyzed. Machine learning projects should therefore always start as a proof of concept. This involves questions such as: Which data represents or affects the correlations the most or what hit rate is achievable with the model and how can it be improved?
Rollout – Go Live:
Once the pilot project has been successfully tested and adapted, the AI solution can be rolled out productively on the line or machine.
We are happy to help you!
Together with our partner paiqo, we offer individual solutions for the design and implementation of cloud-based data platforms in conjunction with state-of-the-art AI algorithms. From anomaly detection, predictive quality and predictive maintenance to AI assistance systems, together we support companies on their way to efficient and future-proof production.